The use of a diamond disc is now a widespread tool among construction professionals for cutting ceramics. Diamond blades are made of a steel core with a crown-like edge formed by a metal alloy with diamond particles, which is where they get their name. But do we really know how they work and how to use a diamond disc in an actual tile installation? We’ll explain it in this article.

Diamond or Diamond-Coated Blade: What It Is and What It’s For
First, we need to understand that these diamond blades are abrasive tools that “cut” by the friction of diamond particles. The diamond particles are embedded in a metal alloy called a binder.
The binder’s function is to hold the diamond particles until they wear out or break. As the binder wears down, it will allow the replacement of the worn diamond with new particles.
This binder function is crucial. If it’s not very resistant to abrasion, it will result in tools with very fast and high-quality cuts, but with a short lifespan.
On the other hand, if the blade is very resistant to abrasion, the worn diamond particles will not be replaced, and the tool will lose its cutting power.
It is then said that the blade has “closed,” has become smooth or “blunted,” and needs to be revived with a cleaning block to continue working.
Diamond Blade: How to Choose It
At RUBI, we have a wide variety of diamond blades. To choose the right one that fits our needs, we must consider the following factors:
- What material are we going to cut?
As mentioned earlier, each material has different hardness and difficulty. In this case, we will need a blade and binder that adapt to the material we are cutting, ensuring the diamond always remains on the surface of the binder for a clean cut.
At RUBI, we make it easy, so we have different colored blades for different materials that can be cut. - What type of cut are we going to make?
Cutting at an angle (mitering) is not the same as making a straight cut. At RUBI, we have special blades for mitering.
This type of cut puts very high lateral pressure on the blade, and not just any blade will give us a good cut. We will need enough thickness to prevent the diamond blade from getting damaged. - Types of Diamond Disc Edge
The edge of the diamond blade can have several finishes. The most common are continuous, segmented, or turbo blades:- Continuous blades: blades with a continuous diamond edge. They are generally used to achieve a finer finish in jobs that require more precision in cutting. Their cutting speed is slower.
- Segmented blades: blades with a segmented diamond edge (separated by gaps) for cutting materials such as brick, stone, granite, etc. They offer the highest cutting speed but produce a rougher finish.
- Turbo (laser) blades: blades with a notched diamond edge. They provide a faster cutting speed than continuous edge blades and a better finish than segmented edge blades. However, they offer a medium finish with medium speed.
- Blade Diameter
There are diamond blades of different diameters on the market. The blade’s diameter determines the depth of cut.
It is essential to match the blade to the cutter we will use. For example, we should never use a 350mm blade in a machine that accepts blades up to 250mm. - Types of Cutting
The cutting mechanics of diamond blades generate high temperatures, leading to two types of cuts depending on cooling methods:- Dry cutting: this type of diamond blade does not need lubrication or water cooling (although it can also be used with water). The tool works solely with the cooling produced by air. This type of cutting is generally done with grinders or angle grinders.
- Wet cutting: this type of diamond blade is cooled with water to lubricate and maintain a stable temperature during cutting. Additionally, it helps clean the diamond blade and remove the dust generated during the process. This provides a more durable and much cleaner, professional cut. This type of cutting is usually done with electric cutters.

Diamond Disc: How to Use It
We must always follow the manufacturer’s recommendations regarding the material to be cut and ensure the blade is not damaged. However, remember to keep these recommendations in mind:
- Check that the blade is not damaged.
- Regularly inspect the blade to ensure there are no cracks, wear, or loss of flatness.
- Ensure the fastening plates are the correct diameter, equal, free of play, and flat.
- Ensure the blade is correctly mounted and securely fastened.
- Verify that the bearings and shaft of the grinder or circular saw are in good condition. Refer to the machine manufacturer’s manual for proper maintenance.
- Respect the maximum operating speed for each blade diameter, as indicated by the manufacturer.
- Never use a wet cutting blade for dry cutting.
- Do not force the blade during the cut; allow it to set its own working pace.
- Never work while obstructing the cutting line or blade path.
- Allow for proper cooling by letting the blade spin freely every few minutes. Do not make long or continuous cuts. The harder the material, the more frequently you should do this.
- When making a wet cut, do not start cutting until the water flow is adequate.
In conclusion, always remember that safety at work is essential, and working with diamond blades is no exception.
Always wear appropriate safety gear: goggles, proper footwear, fitted clothing, hearing protection, and, when necessary, a mask. But undoubtedly, correct use of the blades is crucial to maintaining safety at all times.
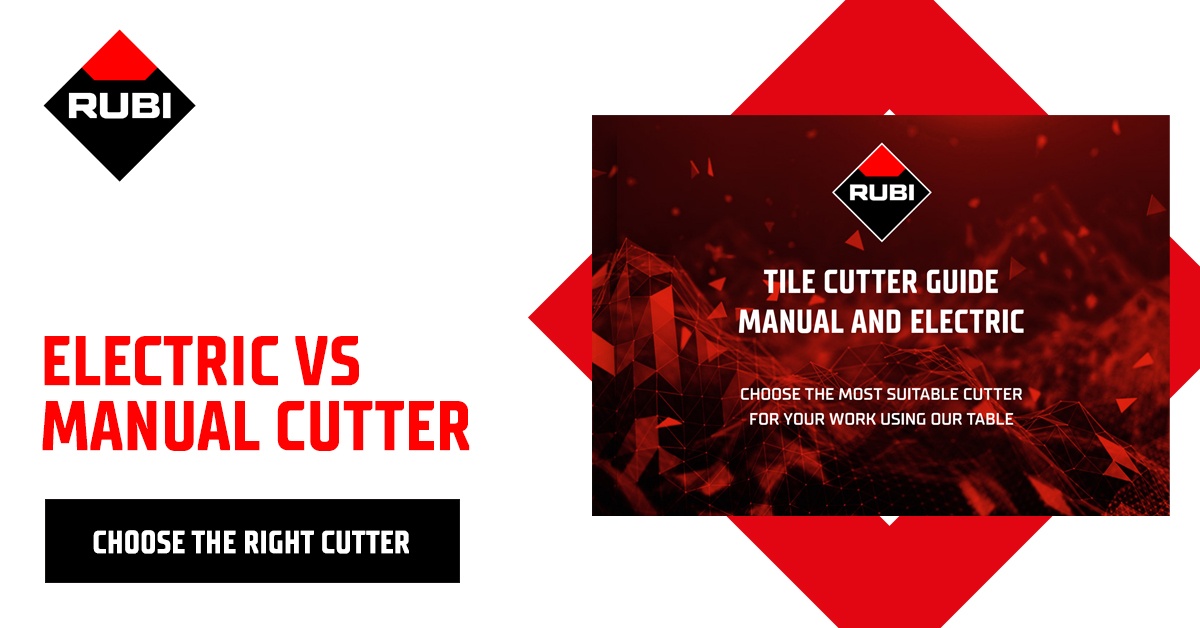
Post a comment