El gres porcelánico se ha convertido en los últimos años en la baldosa cerámica más usada en la construcción. En este artículo explicaremos cuáles son sus características y los motivos que han llevado a este material a convertirse en una tendencia a nivel mundial, la cual apunta a seguir creciendo mucho más en el futuro.
Tipos de gres porcelánico
Baldosas cerámicas
El término «cerámica» proviene de la palabra griega «Kerameicos», que significa «de barro».
Los productos cerámicos son artículos hechos por el hombre, que han sido primero moldeados o modelados usando un amplio número de minerales y rocas, y luego endurecidos por el calor. Esta definición clásica de producto cerámico se puede simplificar como: «objeto moldeado con materias primas naturales plásticas y endurecido permanentemente por el calor». Pero también se puede generalizar como «el producto final de un proceso industrial (proceso cerámico) en el que se transforman y endurecen los materiales de partida (materias primas)».
La baldosa cerámica está hecha con arcillas rojas, marrón o arcilla blanca. La mayoría de baldosas de gres porcelánico están hechas utilizando arcilla blanca.
Una vez que las baldosas se forman con la mezcla de materias primas, entre las que se encuentran las arcillas, caolines, arenas de cuarzos, feldespatos, además de otros materiales ferrosos y agua. Después las mezclas son expuestas a altas temperaturas en hornos.
Proceso cerámico: 5 etapas
El proceso cerámico consta de cinco etapas:
- La selección y preparación de las materias primas.
- La preparación del cuerpo cerámico, que consiste en la preparación de la mezcla, homogenización y amasado.
- El moldeado, que puede hacerse por varios procedimientos.
- El secado.
- La cocción.
Como resultado de todo ello se obtiene el producto cerámico, que deberá pasar controles de calidad.
Todas las etapas son importantes, pero es sin duda la cocción la más crítica porque en esta etapa se consigue realmente el producto cerámico final. El proceso de cocción se realiza a temperaturas superiores a los 900°C, cuando la mayoría de los minerales comunes que entran a formar parte de la pasta son inestables, hasta los 1600°C.
El proceso de enfriamiento posterior también influye mucho en el resultado final en cuanto a calidad, dureza y tensiones internas que pueda presentar el material.
Clases de cerámica
Según la combinación y proporción de materias primas, el proceso de fabricación, y la temperatura y proceso de cocción, obtendremos diferentes clases de cerámica:
- Porosa sin esmalte: la cerámica estructural tipo ladrillos y tejas, ladrillos refractarios y loza.
- Porosa con esmalte o “vidriado”: por ejemplo, la mayólica y loza esmaltadas.
- No porosas sin esmalte o esmaltadas: la porcelana, azulejo, gres y gres porcelánico.

Gres porcelánico: el más usado en la construcción
El gres porcelánico es un material cerámico perteneciente al grupo de los materiales silíceos. La sílice está compuesta, entre otros minerales, por cuarzo y arenas silíceas. Forman parte de este grupo de materiales toda la cerámica, entre la que encontramos el azulejo, el gres, y gres porcelánico.
También el vidrio e incluso el granito. Son materiales que presentan unos niveles de dureza media-alta o muy alta, y algunos pueden también presentar altos índices de abrasividad.
¿Por qué es el material más usado?
La diferencia entre una loseta o baldosa cerámica tradicional, y una de gres porcelánico, es que la mezcla de arcilla y arenas es mucho más refinada y purificada. En consecuencia, las baldosas de porcelánico son mucho más densas que las de cerámica estándar.
Esa mayor densidad hace que sean más resistentes, y por ello son ideales para usarlas en áreas con más desgaste como los suelos. También hace que sean menos absorbentes y más resistentes a las manchas.
También influyen mucho en que el gres porcelánico sea la baldosa cerámica más usada en la construcción, los nuevos medios de fabricación e impresión actuales que permiten formatos hace un tiempo impensables en cuanto a espesores, dimensiones y diseños. El gres porcelánico imitación madera, es un ejemplo de ello.
Cada fabricante cuenta con sus formatos que, actualmente, pueden llegar a ser de hasta 3,60 metros de longitud y 1,60 metros de ancho, con espesores que van desde los 3 a los 12 mm e incluso hasta los 20 o 30 mm para exteriores.
Esto ha abierto un nuevo universo de posibilidades para el gres porcelánico con infinidad de aplicaciones:
- Cualquier tipo de superficies interiores o exteriores en el área comercial y residencial
- Encimeras, suelos, paredes, fachadas, revestimientos, hasta mobiliario.
- Espacios de alto tránsito, de carácter urbano como aceras o piscinas, entre muchas otras opciones.
Características del gres porcelánico
Entre las características del gres porcelánico que lo han llevado a ser utilizado en tantas aplicaciones se encuentran:
- Su alta dureza, siendo prácticamente imposible rayarlo. Podemos incluso cortar encima sin provocar ningún daño, con excepción del cuchillo cerámico que lo podría dañar.
- Una alta resistencia a la abrasión y el desgaste.
- Porosidad muy baja, casi nula, es decir que no absorbe líquidos, de modo que la superficie no se mancha y se mantiene como el primer día. Al tener absorción nula tampoco absorbe aceite, por lo tanto, nunca se manchará.
- Es antiácido y no se estropea con cosas comunes como el zumo de limón o vinagre.
- Es un material higiénico, fácil de limpiar y mantener, haciéndolo apto para el contacto con alimentos. Evita la retención de bacterias y sustancias orgánicas.
- Es antideslizante, ideal para utilizar como pavimento seguro y estable.
- Capacidad de personalización.
- Alta resistencia al frío y al hielo, haciéndolo ideal para exteriores. Al no absorber humedad, no hay posibilidad de rotura por congelación interior del agua.
- Estabilidad cromática. Los colores permanecen inalterables a la exposición solar y agentes atmosféricos, y no se degradan con el tiempo ni pierden su brillo gracias a su resistencia a los rayos UV.
- En caso de exposición a las llamas no produce gases tóxicos ni se quema. Así que podemos poner encima un recipiente salido directamente del fuego sin causar ningún daño.
- Versatilidad con su variedad de colores, acabados, formatos y espesores que se adaptan a las necesidades de cada espacio. Permite colocar el mismo material que utilizamos en la encimera con un grosor distinto para forrar muebles, y así conseguir una continuidad de materiales.
Conclusión
Todos los grandes fabricantes del país están apostando muy fuerte por el porcelánico y sus nuevos formatos, y todo esto ha propiciado que aproximadamente el 80% de la cerámica que se coloca hoy en día sea baldosa de gres porcelánico.
Y teniendo en cuenta todas sus cualidades y posibles aplicaciones que hemos comentado, estamos seguros de que el porcentaje continuará subiendo y el gres porcelánico seguirá siendo la baldosa cerámica más usada en la construcción.
Si quieres informarte acerca de los problemas más comunes al trabajar con gres porcelánico, consulta este artículo.
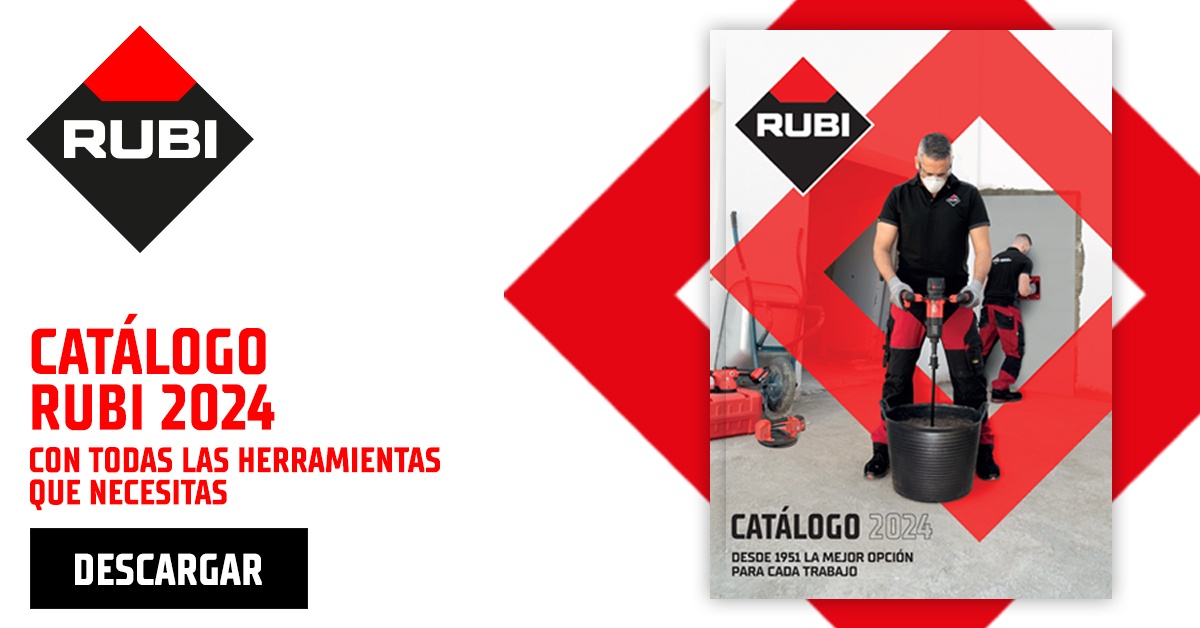
Buenos días, tengo instalado gres porcelanico en el suelo exterior y cerca hay una chimenea de fuego bajo que quema leña. El gres se ha ensuciado, con que producto puedo limpiar.
Hola buenos días Alberto, deberías dirigirte a un fabricante de productos químicos para limpieza Como Fila, nosotros no tenemos nada parecido. Muchas gracias